- 9.9 Hp Gamefisher Outboard Motor
- Gamefisher 9.9 Outboard
- 9 9 H P Gamefisher Outboard Manuals
- 9.9 Gamefisher Outboard Motor Parts
- 9.9 Gamefisher Outboard
- 9.9 Hp Gamefisher Outboard Motor
View and Download Chrysler 9.9 H.P. Service manual online. Outboard motor pdf manual download. Also for: 15 h.p., 250 sailor. View and Download Sears Gamefisher 298.586192 owner's manual online. Outboard Motor 3.0 H.P. Gamefisher 298.586192 outboard motor pdf manual download.

Chrysler / Force / Gamefisher 9.9 / 15 hp Outboard Repair |
The motor we will be dealing with here is a Gamefisher 15hp outboard sold by Sears Roebuck & Co. Model 225.587151 made between 1984 and 1987. This particular motor has a low serial number (in the 1500 range), so was probably made in 85, however the carb has a date of 11-86 on it, so maybe they didn't sell as many as I would expect. The 9.9hp motors were the same basic engine, likely with a different carburetor main jet. These motors were made for Sears after that, but the starter unit was changed.
This motor is rated at 15hp with a RPM of 5100, but a maximum RPM at 5600.
History ;Chrysler started out in the Marine business by making engines for other manufacturers. They started in 1926, by supplying builders like Chris Craft with inboard engines. At one point in the 40's Chrysler had about 40 percent of the marine engine market.
Quote from a former Chrysler marine executive,'We were told that as part of the government bailout, Chrysler had to sell off all it's neonate related businesses and concentrate on it's auto business. I believe we were the last to go. We all knew it was up for sale. It took until'84 to find a buyer for the outboard business. Unfortunately it was Bayliner. When Bayliner took over, it promised to keep the business open for at least 2 years. After the 2 year period it was sold to Brunswick. The rest is history. ' Thanks for the Insight!!!!
When Chrysler finally got out of the Marine business they sold the power boat division to Texas Marine International ( Exec's from the Chrysler Boat Corporation ). Then soon after purchasing the boat company discontinued the powerboats to focus on the sailboat market, but it wasn't long and they folded. Powerboat parts were sold by TMI to Doug Russell Marine, Worcester, Ma.. The Sailboats were sold to to Starwind Parts. Starwind Parts has since sold molds, spare parts, sails, etc. Lone Star boats started out in Grand Prairie, Texas back in the 50's. In 1962 Lone Star moved their manufacturing plant to International Parkway, in Plano, Texas. Chrysler Buys Lone Star in 1965
Chrysler Corp. purchased West Bend's outboard manufacturing in January, 1965. This first year they were known as a Chrysler/West Bend outboard. Chrysler stern drives were sold to Bayliner Boats in 1983 and the outboard division was sold to the Force Outboards division of U.S. Marine - an affiliate of Bayliner - in 1984. Bayliner wanted to start packaging their boats, and the Capri line was introduced to the buying public with 'Force' engines on the transom. At first, they were just Chrysler's with Force stickers. They later came out with their own cowlings and paint scheme to match the Bayliner branding. When Brunswick purchased Bayliner, they inherited the these Force outboards, probably unwanted, and mostly obsolete, engines came with the deal. However Mercury took advantage of the opportunityand ended up with low cost Force engines to factory rig their boats, perhaps an idea of ahead of it's time.
Mercury decided to spruce them up and improve them, with Mercury gear cases/props, CD ignition systems, etc., and market them as 2nd tier engines. I understand, they were actually pretty good, but not really hot performers and with a second tier, 'cheapout' image for the owners. The situation spooked Yamaha and OMC enough that they downgraded their own lines, removing oil injection and other items, so they, too, would have a second tier line. OMC called them the 'Special' engines, with odd ball HP number to set them apart. Yamaha had a designation for theirs also. As clean technology became mandated, this engine had to die, so Mercury dumped it in favor of putting Merc engines on Bayliners, and all their other brands also.
The Force name later turned into the Mariner brand outboards which was introduced in Australia sometime in the early 70's and in the United States in 1976.
Ignition ;This series of motors used a WICO magneto ignition, with points and condensers. Points are set at .020'. These points units were not the most thought out unit as setting them had some challenges and is the wiring screw had another nut to hold the block in place with a second nut to secure the wires, it could be easier. In setting the points, I have found it easiest to reinstall the flywheel nut and screw it down to where it stops on the crankshaft, form here you can use a wrench on the nut and rotate the crankshaft to where the widest part of the cam is in contact with the point rub bar. There may not be any mark on the points cam to indicate where the set location is, if not, then use the flywheel key as that location as it will normally be in the thickest/highest spot. And the critical point is when the points break governed by the ramp up to the high spot.
Later motors from about 1993 on used electronic ignition. Here, if for some reason you need to find Top Dead Center (TDC) it may be easiest to use the old motorcycle method of pulling the spark plug and running a rod down inside the cylinder, pull it over SLOWLY and watch the rod move out, stopping it at the highest point. However there is really no need to worry as there is not much you can do as to timing on these anyway, other than carburetor cam arm roller positioning. Usually in numbering cylinders, the top one would be number ONE.
Flywheel ;One odd thing here is that there are no provisions for using a standard 3 bolt flywheel puller. My method of pulling these flywheels is to back the nut off until the top is just above the threads (protecting them), using a medium heavy hammer (soft brass preferred), wrap your arm around the flywheel, putting a lifting strain on the motor and SHARPLY RAP this nut. Usually this will jar the flywheel loose.
There are three detents in the approximate locations, (as seen in the photo below) which the stamped sheet-metal emergency rope starter plate nestles into to secure this plate after the flywheel nut is tightened down on top of the plate.
The flywheel retainer nut has 7/8' across the flats and uses a wrench of that size to remove it. The flywheel woodruff key was basically a 3/4' diameter (cut in 1/2) .312' wide and 1/8' thick.
Top side of the flywheel | Bottom side of the flywheel |
Carburetor ;These were rather simple carburetors. The one on this motor was a Tillitson model LMB 229B, 6180612 11-86. The internal throat is .875' diameter where it mounts onto the manifold. The one bad thing is getting it off the manifold. The RH nut has not enough room between the carburetor body and the nut to get a standard wrench on unless it has a short handle.
The float bowl needle seat is unique in that it is a green Neoprene ring held in the hole by one loop 'clip' of a coil spring. The needle then is just stainless and has a retracting clip. The float is a soldered brass float. The idle needle is usually backed out 1 1/4 turns. There is a throttle arm roller that is attached by a eccentric bolt, which is used to adjust the link and sync.
The choke is simple and attached to the rod by a spring clip similar to that used by the automotive industry. On the choke plate of the carburetor, it has 3 slight notches that individually engage in a small short standup coil spring that retains the choke in the closest position.
It has a round metal float bowl that is held on by a combo bolt/main-jet (#63) for the 15hp motor and a (#48) for the 9.9hp.
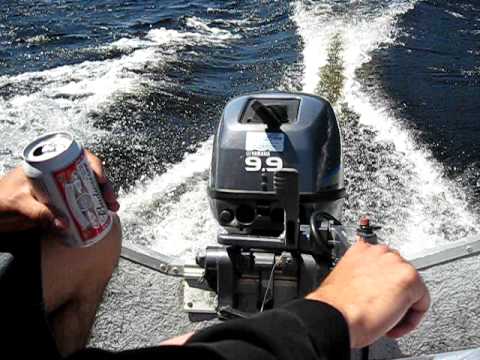
A long threaded bolt on the left side of the mid/forward of the motor and attached to the timing plate linkage is a slow speed stop.
There is no air breather on this carburetor.
It will be a challenge to clean this carburetor and be able to REUSE the float rubber bowl ring seal. Mercury's current part number is 27-F10068 which sells for $2.70 but not normally carried by many dealers, however if you go to a lawnmower shop, Briggs & Stratton's corresponding number is 693981 and sells for $2.60. This seal appears very slightly smaller diameter, so needs to be warmed up in the sun or in HOT WATER or soaked in gasoline, stretch it enough to allow it to stay in the groove in the carburetor's bowl base long enough to install the bowl. Then it has to be pretty tightly fitting on the outer rim otherwise it may leak. So trial and error may be the order of the day when using this seal.
A trick here when using the B&S seal, may be instead of installing the carburetor on the manifold, pumping up the fuel, looking for leaks, I found that if you just attach the fuel line to the carb while it is not bolted to the motor, you can connect the fuel coupler to the motor, hold the carburetor level as on the motor, pump it up and if it leaks, a lot less hassle then to re-adjust this gasket/seal slightly. The problem is the float bowl has only a single thickness of the thin aluminum bowl to seal against the gasket, even a very slight miss-alignment of the gasket can allow fuel to leak out.
Note that this bowl has a flat on one side of the bottom. This flat goes on the pivot pin (inlet) side of the carb body, but not at 90 degrees, as it needs to be aligned with the float hinge base.
One thing that may be beneficial to add, is since the carburetor retainer nuts are 1/4' X 20 TPI (course threads) and hard to really tighten in the positions they are in, you might consider adding lock washers under these nuts at your final assembly.
Fuel Line & coupler ; The fuel line coupler at the motor is a standard old Chrysler quick disconnect style.
Reed Valves ; There are a single set of 2 reeds mounted in a reed plate between the manifold and the front of the block.
Spark Plugs ; The spark plugs that were in this motor were Champion L82Cs.
Fuel Pump ; This fuel pump is specific to Chrysler/Force/Gamefisher motors of this same basic size. Replacement fuel pumps appear to not be available, but parts are to rebuild one. These are a pretty basic diaphragm fuel pump so no surprises when you tear it apart.
View if the fuel pump with the top line going to the carburetor |
The fuel line has a inline small plastic fuel filter, there is another identical one behind the pump and the carburetor. The quick disconnect fuel line is similar to the industrial type oil line connectors and is known as the Chrysler type.
Recoil Starter ;Here is a weird spring system that was carried over from the Chrysler design but only existed for 3 years under the Force name. This spring (#15) is a 1/16' square dual wind (one inside the other, wrapped around a shaft, inside the spool housing). The problem is if the end breaks, (which was the condition I received it in) it is about impossible to refit it to function and the replacement spring along with the plastic base sells for $79.30. However thanks to e-Bay, I found one for $64.95.
A simple and unique system for the spindle gear to be raised and engage the flywheel is a angled slot in the gear that a cross-pin rides in very similar to the small 6-8hp OMCs up to the mid 1980s. As the starter rope is pulled, the gear slides upward on this cross-pin, engaging the flywheel gear.
Replacement starter ropes are 3/16' diameter and 52 ' long. Replacing this rope itself can be a challenge, but explained below.
Exploded view of recoil starter system | Starter spring assembly #FA286970 |
Problems Encountered ;This motor when I got it, had the starter rope frayed badly and worn in two, so no idea of just how it was installed. In the repairs of getting it going, I discovered that a small plastic Vee pulley that is attached to a casting boss on the front of the manifold was a rope guide to facilitate a 90 degree change in the direction the rope came off the spool to going out the front cowling. This plastic pulley was split with 1/2 of it missing. This pulley was held in place on the front of the intake manifold by a 3/16' stainless steel roll pin. In order to remove the pin, the ignition timing plate had to be removed, the roll pin driven down and out of both the upper and lower boss lips. In my driving it out, it went OK out the upper boss , but split lengthwise and part of it hung up slightly inside the lower boss.
Measurements were taken off the broken 1/2 of the pulley and the distance between the upper and lower bosses to come up with a replacement pulley made of Delron. The upper boss was then tapped to 1/4' X 20 TPI and the threads removed on a 1' stainless steel bolt, leaving 1/4' of threads under the head. This bolt then was used to retain the new pulley, leaving in part of the broken roll pin in the bottom boss. The reason for this is the broken part was so tight that I was afraid that if I tried to totally remove it without bottom support, that the bottom aluminum manifold boss would become broken.
The starter rewind spring #15 in the exploded view above is unique in that is is made of 1/16' square spring stock that has a dual spring, being wound as an outer spring transgressing into a inner spring. The inner spring has a crosswise tail that goes inside a slot on the lower end of shaft #12. The outer spring's 90 degree downward tail goes into a plastic base #16 and held in by a small brass clip as seen in the photo on the right above. This plastic base has a slot that straddles and is retained by #21 roll pin.
A problem was encountered when I got it all assembled with the new spring, after the second pull, the spool did not want to recoil. What had happened was that this retainer type roll pin was only held in by being pressed into ONE boss on the rear of part #20 bracket. This long roll pin broke, allowing the spring to unwind, bind it up to where it took a bit of work using two pliers to straighten it back into a usable thing again.
9.9 Hp Gamefisher Outboard Motor
OK, a small boss was fabricated out of scrap aluminum and Heliarc welded onto the front of the #20 as seen in the photo below. The weld slopped over into the hole, which was reamed out using a 1' end mill cutter. Now a new 1/8' hole was drilled, aligning through the existing rear hole and into the new welded on boss. A section of 1/8' drill rod was inserted using both front and rear holes, making for a amore secure attachment. J B Weld was used to secure this rod in place. The front hole was countersunk to allow more epoxy to adhere to the rod's end.
Here you can see the modification & the new drill rod retainer shaft |
Reinstalling Rope ;Not having a service manual, this took a bit of trial and error and there may be a better way, but here is how I did it. It is about mandatory to remove the flywheel to give clearance to remove the upper starter spool bracket #4. Removing the carburetor also helps. The screw #1 just retains the cross pin #13 that retains and activates the starter gear #2. With the spool assembly off the motor, you need to install the new rope into the spool pulley and secure that end. Next slide the spring unit inside the center aluminum tube #19. Slide the gear #2 over the aluminum tube being sure to locate the protruding spring out through and between the forward 'posts' on the #4 bracket.
The new starter spring needs to have the pivot shaft #12 installed inside the spring with the slot in the shaft engaging the lower tail of the inner spring. Locate the cross pin holes in the tube and the upper shaft end, by viewing them in the gear bevel slot. Install the retainer pin #13 and tighten the #1 screw. Try to align the bottom plastic spring base slot so it will slid over the #21 roll pin in the lower bracket. Manipulate this assembly down under the timing plate cam and the plastic base slot onto the roll pin as you slide everything into place. Re-install the screws retaining the #4 bracket.
You are now trying to wind the rope onto the spool while the rewind spring is under tension and getting greater as the number of coils are wound onto the spool.
Have the rope coming out to the right of the spool as seen in the photo below. Poke the loose rope end to the left inward/under the starter gear, but above the spool so you can get ahold of this rope's tail, push the rope down, letting it wind onto the spool while still maintaining tension on this rope. Pull the loose end of the rope, rotating the spool Counter Clockwise. Keep doing this for about 5 or 6 revolutions or until the rope completely fills the spool, all the while maintaining tension on the loose end of the rope.
Be sure to ALWAYS rotate the spoolCOUNTER CLOCKWISE. This is IMPORTANT as you WILL ruin the spring's outer retention tail if you rotate it otherwise.Repeat the poking the loose end of the rope behind and out on the other side of the spool. You may need to do this 2 or 3 times so you apply enough spring rewind tension on the spool. Test this tension by using your finger as a pivot point at the location of the small Delron pulley, so that it will retract the starter pull knob back to the front of the cowling as when the rope would be let go of as if you were trying to start the motor.
If you are satisfied there is enough tension to pull the starter knob back and tight against the cowling, (not enough tension here will allow the starter gear to not retract, allowing the flywheel gear teeth to chew parts off the top of the plastic gear teeth when it starts). Then pull the rope out again, and hold the spool (under spring tension), now poke the rope through as before, but this time also poke it behind the small pulley (home made Delron one shown below) and out through the front cowling rope hole as also shown in the photo below.
You now can test it better for retractability, but remember there will need to be a few inches to attach the pull handle onto the rope with. If it looks OK, pull out another couple of feet and tie a overhand knot in this rope to temporarily secure it so you don't have to fight tension as you install the pull handle.
When you are finished with a NEW starter rope, the rope will fill the spool to it's outer limits, but this will compact down some after usage.
Whitney houston discography torrent. The photo below shows an older motor which uses points and condensers.
Here you can see the arrangement of winding the rope & the cowling front latch to the right of the rope going out the front |
No Provisions for Electric Starter ;As stated, this being a utility motor, there are no provisions for electric starter on this motor.
Throttle System ;This twist grip throttle works reverse rotation from the OMC motors, as counter clockwise slows the motor. It appears to have been made to accept remote controls.
Kill Button ;This kill button has two male spade crimp connectors coming off the rear. This is just a grounding device for shorting out the points to stop the motor. You will notice the light gray and blue female spade connectors on the kill button switch behind the cowling latchin the photo below. This part is No Longer Available as a replacement item.
The rubber covering on this button on the motor that I was working on was cracked/broken enough that what was left (but still functioning) could easily become broken off, loosing the inner metal contact, making it inoperative. The shade-tree repair was to use some black latex caulking to bond these loose parts together.
Shifting Lever ;The shifting lever is mounted on the lower front panel under the starter handle. It moves horizontally to change the gears. There is a starter lock out system so the motor can not be starter in either gear, only neutral. This interlock is indicated by the red arrow in the photo below. You can pull the starter rope in any shift position, but the interlock does not allow the starter pinion gear to raise to engage the flywheel gear unless the shifting lever is in neutral. However many fishermen have been known to remove this feature.
In the photo below you can just see the top corner of the cowling latch at the right of the red arrow. The purple arrow points to the slow speed stop adjustment screw. On the right is the kill button directly above the fuel coupler. On the left, the choke wire is just that a wire with a loop on the front. You will also notice the black felt marked arrow on the top of the spool as a reminder to anyone who may later need to replace the starter rope.
Front view of the assembled motor with cowling off |
Tilt Lever ;There is a white plastic horizontal rotating lever/knob unit on the port side of the tilt shaft that locks/unlocks the motor allowing it to be tilted up. On starboard side once the motor is up a spring loaded latch snaps a side-plate up holding it. To lower, this latch needs to be depressed.
Transom Clamp Screws ;These are standard 1/2' X 13 TPI or 1/2' National Course threads.
Replace Water Pump ;To remove the lower unit, unbolt the four 7/16' size bolt heads from the lower unit at the exhaust housing unit juncture, allowing it to drop down enough to reach in to be able to unscrew the single 5/32' Allen head screw that connects the upper shifting lever from the lower one (as seen in the LH photo below). With this screw removed, the lower unit, should now easily drop down to access the water pump which is bolted on top of the lower unit.

Chrysler / Force / Gamefisher 9.9 / 15 hp Outboard Repair |
The motor we will be dealing with here is a Gamefisher 15hp outboard sold by Sears Roebuck & Co. Model 225.587151 made between 1984 and 1987. This particular motor has a low serial number (in the 1500 range), so was probably made in 85, however the carb has a date of 11-86 on it, so maybe they didn't sell as many as I would expect. The 9.9hp motors were the same basic engine, likely with a different carburetor main jet. These motors were made for Sears after that, but the starter unit was changed.
This motor is rated at 15hp with a RPM of 5100, but a maximum RPM at 5600.
History ;Chrysler started out in the Marine business by making engines for other manufacturers. They started in 1926, by supplying builders like Chris Craft with inboard engines. At one point in the 40's Chrysler had about 40 percent of the marine engine market.
Quote from a former Chrysler marine executive,'We were told that as part of the government bailout, Chrysler had to sell off all it's neonate related businesses and concentrate on it's auto business. I believe we were the last to go. We all knew it was up for sale. It took until'84 to find a buyer for the outboard business. Unfortunately it was Bayliner. When Bayliner took over, it promised to keep the business open for at least 2 years. After the 2 year period it was sold to Brunswick. The rest is history. ' Thanks for the Insight!!!!
When Chrysler finally got out of the Marine business they sold the power boat division to Texas Marine International ( Exec's from the Chrysler Boat Corporation ). Then soon after purchasing the boat company discontinued the powerboats to focus on the sailboat market, but it wasn't long and they folded. Powerboat parts were sold by TMI to Doug Russell Marine, Worcester, Ma.. The Sailboats were sold to to Starwind Parts. Starwind Parts has since sold molds, spare parts, sails, etc. Lone Star boats started out in Grand Prairie, Texas back in the 50's. In 1962 Lone Star moved their manufacturing plant to International Parkway, in Plano, Texas. Chrysler Buys Lone Star in 1965
Chrysler Corp. purchased West Bend's outboard manufacturing in January, 1965. This first year they were known as a Chrysler/West Bend outboard. Chrysler stern drives were sold to Bayliner Boats in 1983 and the outboard division was sold to the Force Outboards division of U.S. Marine - an affiliate of Bayliner - in 1984. Bayliner wanted to start packaging their boats, and the Capri line was introduced to the buying public with 'Force' engines on the transom. At first, they were just Chrysler's with Force stickers. They later came out with their own cowlings and paint scheme to match the Bayliner branding. When Brunswick purchased Bayliner, they inherited the these Force outboards, probably unwanted, and mostly obsolete, engines came with the deal. However Mercury took advantage of the opportunityand ended up with low cost Force engines to factory rig their boats, perhaps an idea of ahead of it's time.
Mercury decided to spruce them up and improve them, with Mercury gear cases/props, CD ignition systems, etc., and market them as 2nd tier engines. I understand, they were actually pretty good, but not really hot performers and with a second tier, 'cheapout' image for the owners. The situation spooked Yamaha and OMC enough that they downgraded their own lines, removing oil injection and other items, so they, too, would have a second tier line. OMC called them the 'Special' engines, with odd ball HP number to set them apart. Yamaha had a designation for theirs also. As clean technology became mandated, this engine had to die, so Mercury dumped it in favor of putting Merc engines on Bayliners, and all their other brands also.
The Force name later turned into the Mariner brand outboards which was introduced in Australia sometime in the early 70's and in the United States in 1976.
Ignition ;This series of motors used a WICO magneto ignition, with points and condensers. Points are set at .020'. These points units were not the most thought out unit as setting them had some challenges and is the wiring screw had another nut to hold the block in place with a second nut to secure the wires, it could be easier. In setting the points, I have found it easiest to reinstall the flywheel nut and screw it down to where it stops on the crankshaft, form here you can use a wrench on the nut and rotate the crankshaft to where the widest part of the cam is in contact with the point rub bar. There may not be any mark on the points cam to indicate where the set location is, if not, then use the flywheel key as that location as it will normally be in the thickest/highest spot. And the critical point is when the points break governed by the ramp up to the high spot.
Later motors from about 1993 on used electronic ignition. Here, if for some reason you need to find Top Dead Center (TDC) it may be easiest to use the old motorcycle method of pulling the spark plug and running a rod down inside the cylinder, pull it over SLOWLY and watch the rod move out, stopping it at the highest point. However there is really no need to worry as there is not much you can do as to timing on these anyway, other than carburetor cam arm roller positioning. Usually in numbering cylinders, the top one would be number ONE.
Flywheel ;One odd thing here is that there are no provisions for using a standard 3 bolt flywheel puller. My method of pulling these flywheels is to back the nut off until the top is just above the threads (protecting them), using a medium heavy hammer (soft brass preferred), wrap your arm around the flywheel, putting a lifting strain on the motor and SHARPLY RAP this nut. Usually this will jar the flywheel loose.
There are three detents in the approximate locations, (as seen in the photo below) which the stamped sheet-metal emergency rope starter plate nestles into to secure this plate after the flywheel nut is tightened down on top of the plate.
The flywheel retainer nut has 7/8' across the flats and uses a wrench of that size to remove it. The flywheel woodruff key was basically a 3/4' diameter (cut in 1/2) .312' wide and 1/8' thick.
Top side of the flywheel | Bottom side of the flywheel |
Carburetor ;These were rather simple carburetors. The one on this motor was a Tillitson model LMB 229B, 6180612 11-86. The internal throat is .875' diameter where it mounts onto the manifold. The one bad thing is getting it off the manifold. The RH nut has not enough room between the carburetor body and the nut to get a standard wrench on unless it has a short handle.
The float bowl needle seat is unique in that it is a green Neoprene ring held in the hole by one loop 'clip' of a coil spring. The needle then is just stainless and has a retracting clip. The float is a soldered brass float. The idle needle is usually backed out 1 1/4 turns. There is a throttle arm roller that is attached by a eccentric bolt, which is used to adjust the link and sync.
The choke is simple and attached to the rod by a spring clip similar to that used by the automotive industry. On the choke plate of the carburetor, it has 3 slight notches that individually engage in a small short standup coil spring that retains the choke in the closest position.
It has a round metal float bowl that is held on by a combo bolt/main-jet (#63) for the 15hp motor and a (#48) for the 9.9hp.
A long threaded bolt on the left side of the mid/forward of the motor and attached to the timing plate linkage is a slow speed stop.
There is no air breather on this carburetor.
It will be a challenge to clean this carburetor and be able to REUSE the float rubber bowl ring seal. Mercury's current part number is 27-F10068 which sells for $2.70 but not normally carried by many dealers, however if you go to a lawnmower shop, Briggs & Stratton's corresponding number is 693981 and sells for $2.60. This seal appears very slightly smaller diameter, so needs to be warmed up in the sun or in HOT WATER or soaked in gasoline, stretch it enough to allow it to stay in the groove in the carburetor's bowl base long enough to install the bowl. Then it has to be pretty tightly fitting on the outer rim otherwise it may leak. So trial and error may be the order of the day when using this seal.
A trick here when using the B&S seal, may be instead of installing the carburetor on the manifold, pumping up the fuel, looking for leaks, I found that if you just attach the fuel line to the carb while it is not bolted to the motor, you can connect the fuel coupler to the motor, hold the carburetor level as on the motor, pump it up and if it leaks, a lot less hassle then to re-adjust this gasket/seal slightly. The problem is the float bowl has only a single thickness of the thin aluminum bowl to seal against the gasket, even a very slight miss-alignment of the gasket can allow fuel to leak out.
Note that this bowl has a flat on one side of the bottom. This flat goes on the pivot pin (inlet) side of the carb body, but not at 90 degrees, as it needs to be aligned with the float hinge base.
One thing that may be beneficial to add, is since the carburetor retainer nuts are 1/4' X 20 TPI (course threads) and hard to really tighten in the positions they are in, you might consider adding lock washers under these nuts at your final assembly.
Fuel Line & coupler ; The fuel line coupler at the motor is a standard old Chrysler quick disconnect style.
Reed Valves ; There are a single set of 2 reeds mounted in a reed plate between the manifold and the front of the block.
Spark Plugs ; The spark plugs that were in this motor were Champion L82Cs.
Fuel Pump ; This fuel pump is specific to Chrysler/Force/Gamefisher motors of this same basic size. Replacement fuel pumps appear to not be available, but parts are to rebuild one. These are a pretty basic diaphragm fuel pump so no surprises when you tear it apart.
View if the fuel pump with the top line going to the carburetor |
The fuel line has a inline small plastic fuel filter, there is another identical one behind the pump and the carburetor. The quick disconnect fuel line is similar to the industrial type oil line connectors and is known as the Chrysler type.
Recoil Starter ;Here is a weird spring system that was carried over from the Chrysler design but only existed for 3 years under the Force name. This spring (#15) is a 1/16' square dual wind (one inside the other, wrapped around a shaft, inside the spool housing). The problem is if the end breaks, (which was the condition I received it in) it is about impossible to refit it to function and the replacement spring along with the plastic base sells for $79.30. However thanks to e-Bay, I found one for $64.95.
A simple and unique system for the spindle gear to be raised and engage the flywheel is a angled slot in the gear that a cross-pin rides in very similar to the small 6-8hp OMCs up to the mid 1980s. As the starter rope is pulled, the gear slides upward on this cross-pin, engaging the flywheel gear.
Replacement starter ropes are 3/16' diameter and 52 ' long. Replacing this rope itself can be a challenge, but explained below.
Exploded view of recoil starter system | Starter spring assembly #FA286970 |
Problems Encountered ;This motor when I got it, had the starter rope frayed badly and worn in two, so no idea of just how it was installed. In the repairs of getting it going, I discovered that a small plastic Vee pulley that is attached to a casting boss on the front of the manifold was a rope guide to facilitate a 90 degree change in the direction the rope came off the spool to going out the front cowling. This plastic pulley was split with 1/2 of it missing. This pulley was held in place on the front of the intake manifold by a 3/16' stainless steel roll pin. In order to remove the pin, the ignition timing plate had to be removed, the roll pin driven down and out of both the upper and lower boss lips. In my driving it out, it went OK out the upper boss , but split lengthwise and part of it hung up slightly inside the lower boss.
Measurements were taken off the broken 1/2 of the pulley and the distance between the upper and lower bosses to come up with a replacement pulley made of Delron. The upper boss was then tapped to 1/4' X 20 TPI and the threads removed on a 1' stainless steel bolt, leaving 1/4' of threads under the head. This bolt then was used to retain the new pulley, leaving in part of the broken roll pin in the bottom boss. The reason for this is the broken part was so tight that I was afraid that if I tried to totally remove it without bottom support, that the bottom aluminum manifold boss would become broken.
The starter rewind spring #15 in the exploded view above is unique in that is is made of 1/16' square spring stock that has a dual spring, being wound as an outer spring transgressing into a inner spring. The inner spring has a crosswise tail that goes inside a slot on the lower end of shaft #12. The outer spring's 90 degree downward tail goes into a plastic base #16 and held in by a small brass clip as seen in the photo on the right above. This plastic base has a slot that straddles and is retained by #21 roll pin.
A problem was encountered when I got it all assembled with the new spring, after the second pull, the spool did not want to recoil. What had happened was that this retainer type roll pin was only held in by being pressed into ONE boss on the rear of part #20 bracket. This long roll pin broke, allowing the spring to unwind, bind it up to where it took a bit of work using two pliers to straighten it back into a usable thing again.
9.9 Hp Gamefisher Outboard Motor
OK, a small boss was fabricated out of scrap aluminum and Heliarc welded onto the front of the #20 as seen in the photo below. The weld slopped over into the hole, which was reamed out using a 1' end mill cutter. Now a new 1/8' hole was drilled, aligning through the existing rear hole and into the new welded on boss. A section of 1/8' drill rod was inserted using both front and rear holes, making for a amore secure attachment. J B Weld was used to secure this rod in place. The front hole was countersunk to allow more epoxy to adhere to the rod's end.
Here you can see the modification & the new drill rod retainer shaft |
Reinstalling Rope ;Not having a service manual, this took a bit of trial and error and there may be a better way, but here is how I did it. It is about mandatory to remove the flywheel to give clearance to remove the upper starter spool bracket #4. Removing the carburetor also helps. The screw #1 just retains the cross pin #13 that retains and activates the starter gear #2. With the spool assembly off the motor, you need to install the new rope into the spool pulley and secure that end. Next slide the spring unit inside the center aluminum tube #19. Slide the gear #2 over the aluminum tube being sure to locate the protruding spring out through and between the forward 'posts' on the #4 bracket.
The new starter spring needs to have the pivot shaft #12 installed inside the spring with the slot in the shaft engaging the lower tail of the inner spring. Locate the cross pin holes in the tube and the upper shaft end, by viewing them in the gear bevel slot. Install the retainer pin #13 and tighten the #1 screw. Try to align the bottom plastic spring base slot so it will slid over the #21 roll pin in the lower bracket. Manipulate this assembly down under the timing plate cam and the plastic base slot onto the roll pin as you slide everything into place. Re-install the screws retaining the #4 bracket.
You are now trying to wind the rope onto the spool while the rewind spring is under tension and getting greater as the number of coils are wound onto the spool.
Have the rope coming out to the right of the spool as seen in the photo below. Poke the loose rope end to the left inward/under the starter gear, but above the spool so you can get ahold of this rope's tail, push the rope down, letting it wind onto the spool while still maintaining tension on this rope. Pull the loose end of the rope, rotating the spool Counter Clockwise. Keep doing this for about 5 or 6 revolutions or until the rope completely fills the spool, all the while maintaining tension on the loose end of the rope.
Be sure to ALWAYS rotate the spoolCOUNTER CLOCKWISE. This is IMPORTANT as you WILL ruin the spring's outer retention tail if you rotate it otherwise.Repeat the poking the loose end of the rope behind and out on the other side of the spool. You may need to do this 2 or 3 times so you apply enough spring rewind tension on the spool. Test this tension by using your finger as a pivot point at the location of the small Delron pulley, so that it will retract the starter pull knob back to the front of the cowling as when the rope would be let go of as if you were trying to start the motor.
If you are satisfied there is enough tension to pull the starter knob back and tight against the cowling, (not enough tension here will allow the starter gear to not retract, allowing the flywheel gear teeth to chew parts off the top of the plastic gear teeth when it starts). Then pull the rope out again, and hold the spool (under spring tension), now poke the rope through as before, but this time also poke it behind the small pulley (home made Delron one shown below) and out through the front cowling rope hole as also shown in the photo below.
You now can test it better for retractability, but remember there will need to be a few inches to attach the pull handle onto the rope with. If it looks OK, pull out another couple of feet and tie a overhand knot in this rope to temporarily secure it so you don't have to fight tension as you install the pull handle.
When you are finished with a NEW starter rope, the rope will fill the spool to it's outer limits, but this will compact down some after usage.
Whitney houston discography torrent. The photo below shows an older motor which uses points and condensers.
Here you can see the arrangement of winding the rope & the cowling front latch to the right of the rope going out the front |
No Provisions for Electric Starter ;As stated, this being a utility motor, there are no provisions for electric starter on this motor.
Throttle System ;This twist grip throttle works reverse rotation from the OMC motors, as counter clockwise slows the motor. It appears to have been made to accept remote controls.
Kill Button ;This kill button has two male spade crimp connectors coming off the rear. This is just a grounding device for shorting out the points to stop the motor. You will notice the light gray and blue female spade connectors on the kill button switch behind the cowling latchin the photo below. This part is No Longer Available as a replacement item.
The rubber covering on this button on the motor that I was working on was cracked/broken enough that what was left (but still functioning) could easily become broken off, loosing the inner metal contact, making it inoperative. The shade-tree repair was to use some black latex caulking to bond these loose parts together.
Shifting Lever ;The shifting lever is mounted on the lower front panel under the starter handle. It moves horizontally to change the gears. There is a starter lock out system so the motor can not be starter in either gear, only neutral. This interlock is indicated by the red arrow in the photo below. You can pull the starter rope in any shift position, but the interlock does not allow the starter pinion gear to raise to engage the flywheel gear unless the shifting lever is in neutral. However many fishermen have been known to remove this feature.
In the photo below you can just see the top corner of the cowling latch at the right of the red arrow. The purple arrow points to the slow speed stop adjustment screw. On the right is the kill button directly above the fuel coupler. On the left, the choke wire is just that a wire with a loop on the front. You will also notice the black felt marked arrow on the top of the spool as a reminder to anyone who may later need to replace the starter rope.
Front view of the assembled motor with cowling off |
Tilt Lever ;There is a white plastic horizontal rotating lever/knob unit on the port side of the tilt shaft that locks/unlocks the motor allowing it to be tilted up. On starboard side once the motor is up a spring loaded latch snaps a side-plate up holding it. To lower, this latch needs to be depressed.
Transom Clamp Screws ;These are standard 1/2' X 13 TPI or 1/2' National Course threads.
Replace Water Pump ;To remove the lower unit, unbolt the four 7/16' size bolt heads from the lower unit at the exhaust housing unit juncture, allowing it to drop down enough to reach in to be able to unscrew the single 5/32' Allen head screw that connects the upper shifting lever from the lower one (as seen in the LH photo below). With this screw removed, the lower unit, should now easily drop down to access the water pump which is bolted on top of the lower unit.
Gamefisher 9.9 Outboard
The RH photo below shows the water pump attached to the lower unit. It appears that this pump housing is made of the same fiberglass reinforced material as the prop. One good thing about this water pump unit is that the rear slip fit connection to the outlet water tube to the block is that it has a tapered upper end and is deep enough that there is no problem of getting a miss-alignment or leaky seal here.
Here the lower unit is unbolted from the exhaust housing, exposing the Allen head shifting rod connector screw | Here you can see the water pump. Note the long tapered funnel that accepts the water outlet tube to the block |
Do not turn the lower shifting rod either in or out during your impeller replacement as this lower rod's adjustment may be critical for proper placement of the shifting sliding clutch dog. If you do have to remove it, the suggestion would be to turn it in (clockwise) as far as it will go, BUT COUNT the revolutions from your starting location to the bottomed out position. This will give you a reference to return to later on.
Gear Oil ;On the starboard side of the lower unit (gearbox) you will see two large slotted flat headed screws. The upper one is a fill level indicator. The lower screw is a fill screw. These screws have a plastic washer/seal under the heads. To check/replace the oil, unscrew the top screw, if any gear oil comes out it is full, if not then replace this screw and unscrew the lower one. Be careful when removing this one and it may be best to have a container under it to catch any spilled oil.
Unscrew this lower screw, but as it just clears the threads, hesitate, slightly crack the opening and watch for what is going to drain out first. If it is golden or blue, even blackish color, fine. If it has a thick creamy color, you have water intrusion, which is not good. This could be caused by leaky shaft seals or even the drain/fill screws being loose or the plastic washer/seal under the screw heads needs to be replaced.
If it is badly contaminated, you will need to drain and flush the gearbox out with Kerosene, check for leakage and repair that before refilling. If however you concluded that the leak was coming from the washer/seals under the screw heads, replace them and refill the gearbox with new SAE 90 weight gear oil. If you had any water intrusion, you may consider checking for more water occasionally until you are satisfied you have corrected the problem or need to do so.
Refilling is best accomplished by using a outboard motor gear oil pump bottle. These are designed for outboard motors and have a flexible plastic tube mounted in a pump cap on a quart bottle. These tubes come with different size threads to accommodate different motors. These motors use the same standard size as Johnson and Evinrude motors use.
In use, you remove the upper and lower screws, insert the pump tube into the lower threaded hole, pump oil in until it exits out the top hole. This is the full level. Now a trick, screw the upper screw in and tighten it before you remove the lower pump unit. This helps create a slight vacuum so you have a few seconds to get the pump unscrewed from the lower threads and get the plug screw back in creating a lesser oily mess. Clean up any spilled oil and you are ready to go.
Propeller ;These propellers are 3 blade, are 8 X 8 1/4' RH and appear to be made of a fiberglass impregnated material. They are held onto the prop shaft by a splined plastic insert in the prop that mates with the splined .550' diameter prop-shaft. There is a securing stainless steel retainer pin 3/16' X .910' long, that just keeps the prop from moving rearward. To top this off, there is a nose cone cap that is just slid onto the 3/8' unthreaded end of the prop-shaft and secured by a cotter pin, this cap holds the. This cap holds the retainer pin from falling out.
Replacement Parts ;Sears apparently sold off all their remaining spare parts about the year 2010 tohttp://www.marineengine.com/parts/parts.html. This is a large company that also sells Mercury and Force parts, so these parts added to their inventory. Older Mercury parts are expensive. These Force / Gamfefisher parts are no different, but Marine Engine seems to have a fairly good inventory on hand.
Observations ;These motors appear to be nothing fancy, but more of a utility workhorse type motor. The only thing I see wrong with this motor that I was worked on was the weakly designed recoil starter spool spring. However if you take into consideration that at the time of this repair, the motor was 27 years old, maybe it wasn't that bad after all. By looking at the parts drawings, this was changed to a separate overhead mounted starter unit in 1988, and then later changed again.
9 9 H P Gamefisher Outboard Manuals
The owner of this motor says it pushes their 12' aluminum boat faster than his equivalent OMC motors. So an observation is the prop's smaller diameter and slightly less pitch than the OMCs. When OMC goes to their 15hp motors they stay the same diameter but lessen the pitch. This allows the motor to rev about 1000 higher RPM to gain HP.
Maybe this motor was designed with a smaller prop, but allowing the RPM to increase which relates also to higher HP. If this is the case, then the problem would be this motor has less thrust at a lower RPM, but being more designed to be used on lighter boats, where the OMCs could be used on light boats, but also as a kicker motor pushing larger boats at a lesser RPM at a fishing speed.
In many industries where competition is heavy, patent infringements could become expensive, and some designs may look fine on paper, and may function while parts are new, but over time, metal fatigue and wear among other things can take their toll. Again any improvements need to not copy a competitor's design, so you may find a few weak links pop up later. And then there are some operators who seem to have problems no matter what they touch.
Copyright © 2013 - 2020 LeeRoy Wisner All Rights Reserved
<>
<>
Back to the Main Ramblings Page
9.9 Gamefisher Outboard Motor Parts
9.9 Gamefisher Outboard
Originated 05-02-2013, Last updated 11-10-2020
Contact the author
9.9 Hp Gamefisher Outboard Motor
http://www.maxrules.com/ChryslerModels/9p9_15.html